RECYCLING PROCESS
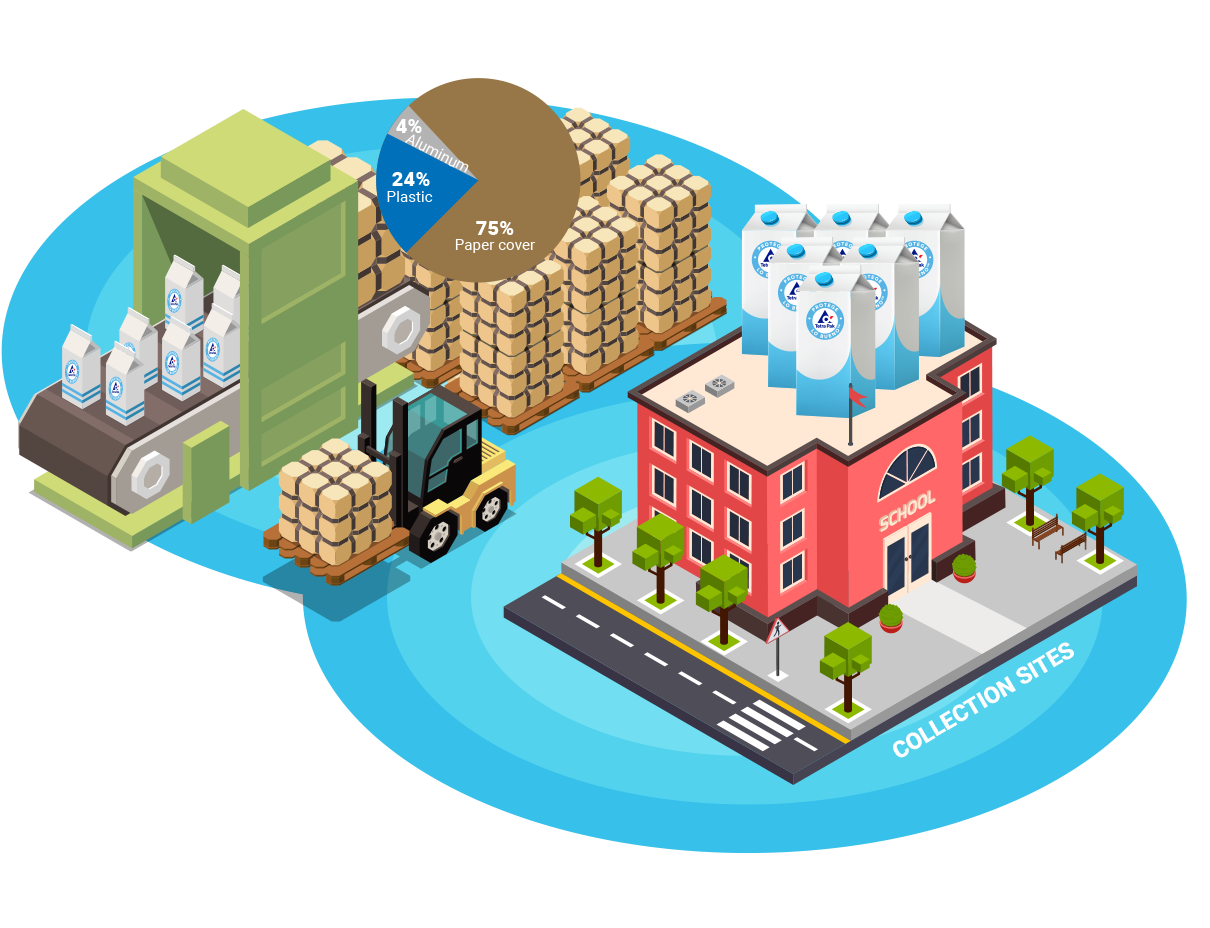
Milk cartons will be collected and taken to the Paper Recycling factory.
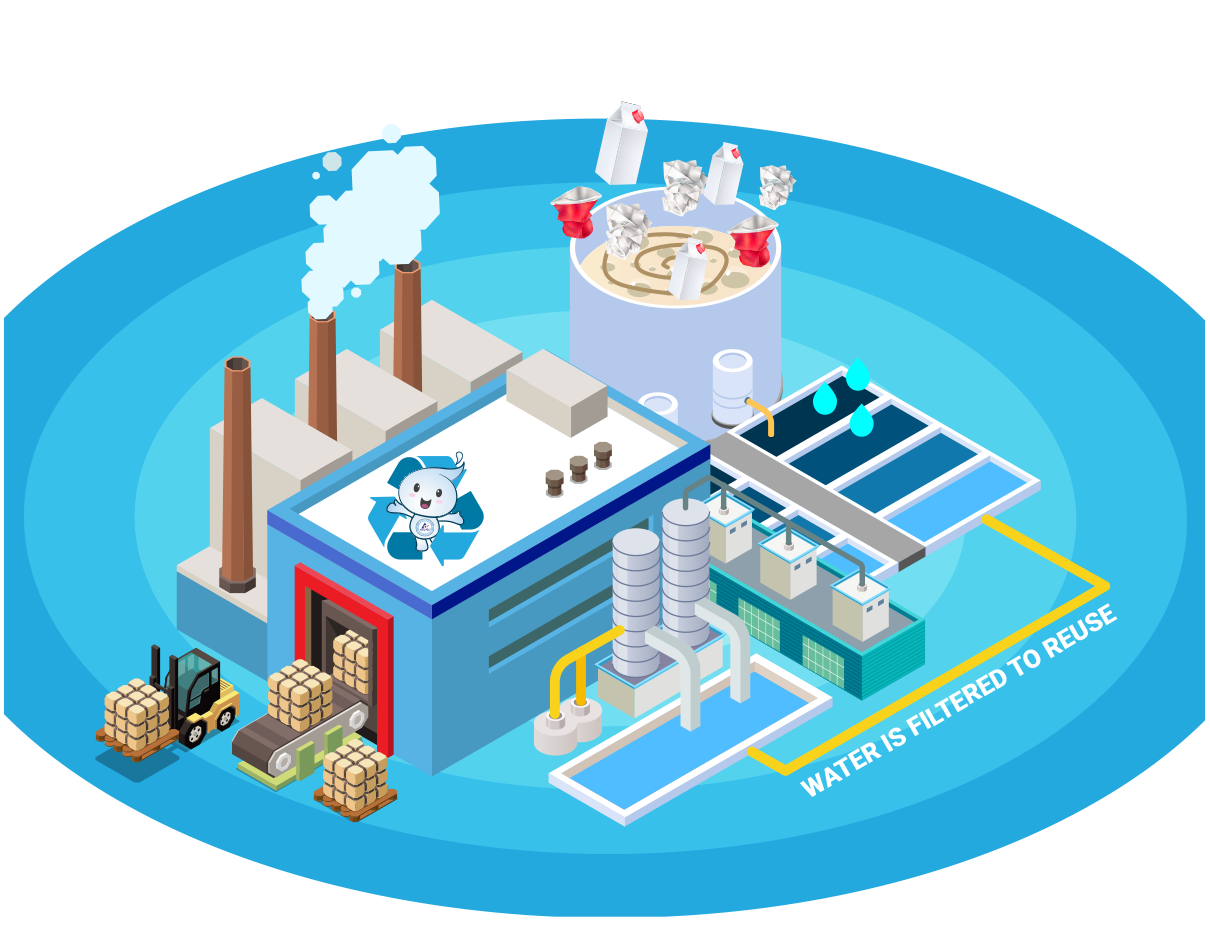
At the factory, the collected milk cartons will be removed from the parcel and transferred to specialized hydraulic to separate and recover the pulp, while keeping intact aluminum and plastic.
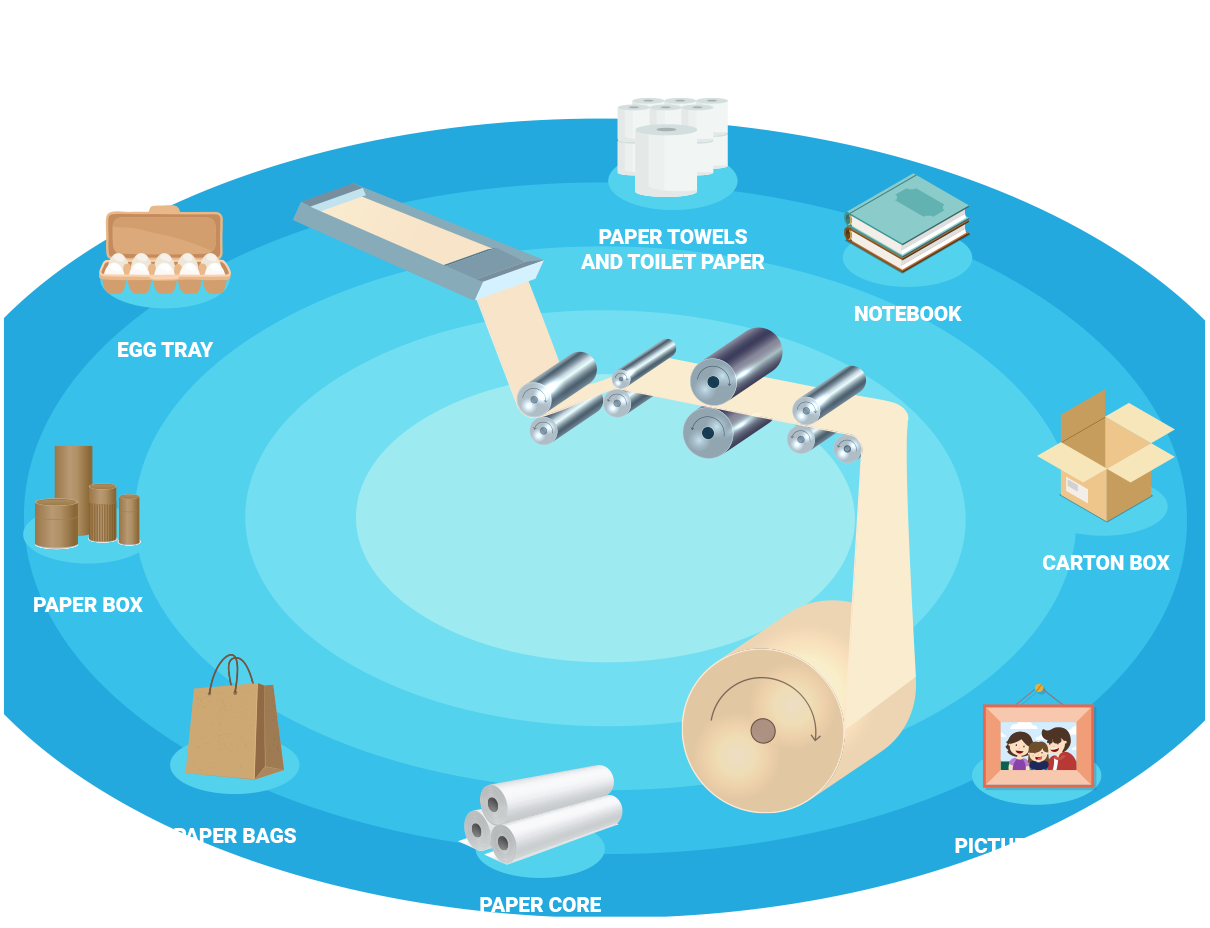
The pulp is carefully selected and removed contaminant, and then it will be shaped paper tape and dried. The finished paper rolls are used to make products such as cartons and recycled paper, etc.
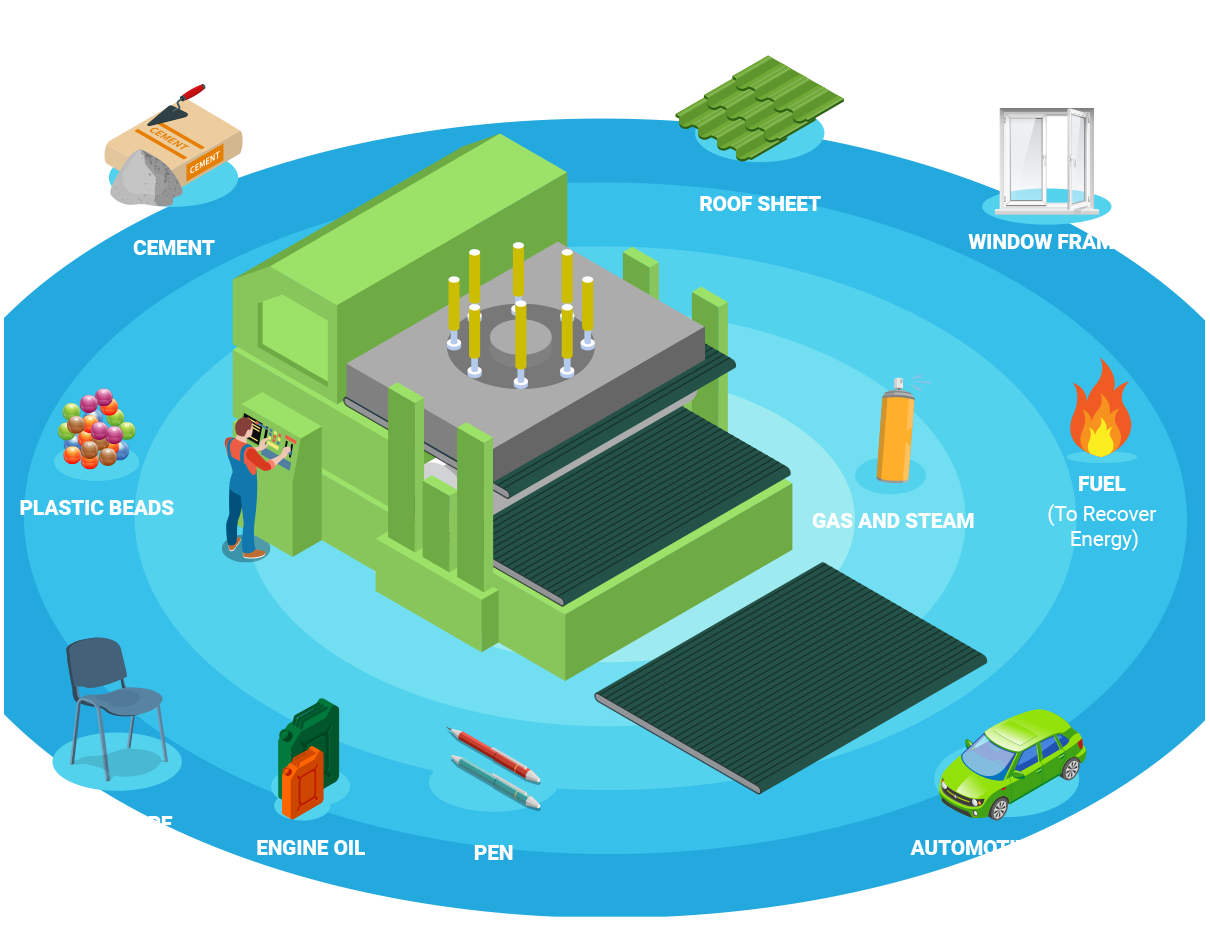
Aluminum and plastic that are separated after the processor will be cleaned contaminant again before transferring through a conveyor belt to a drying cabinet. In the drying cabinet, aluminum and plastic are dried and humidity is only 8%. After drying, the material is put into a shredding machine before being put into press heat at a temperature of 150 degrees Celsius (1500 C), pressing with a force of 80 tons per one square meter for 8 minutes to form thin pieces with 6mm thick. To help the uniform roof in weight, the material will be divided into 16kg every bag and each complete roof will weigh about 14-15kg. Immediately after leaving the hot pressing machine, the roof sheets are transferred to corrugated press and cold-pressed to shape the product. And finally, it will be cutting according to the size and check the finished product before finishing.